ABC Analysis in Logistics: A Comprehensive Guide
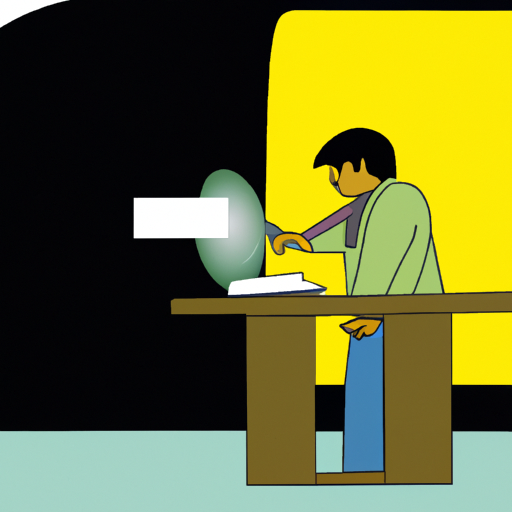
Logistics and inventory management are crucial aspects of any business. Efficient management of inventory can lead to significant cost savings and improved customer satisfaction. One of the methodologies that have gained prominence in inventory management is the ABC analysis. But what exactly is ABC analysis in logistics, and how can it benefit businesses?
What is ABC Analysis?
ABC analysis is a method of categorizing inventory items based on their significance and importance. It's derived from the Pareto Principle, often referred to as the 80/20 rule. This principle suggests that 80% of the consequences come from 20% of the causes. In the context of inventory, it means that a small percentage of items (Category A) account for a large percentage of the value or sales.
Categories in ABC Analysis:
- Category A: These are high-value items that may constitute only 20% of the inventory but contribute to 80% of the revenue. They require tight control and regular review.
- Category B: These items are of medium importance, representing around 30% of the inventory and contributing to about 15% of the revenue.
- Category C: These are the most numerous but contribute the least to revenue. They represent about 50% of the inventory but only 5% of the revenue.
Importance of ABC Analysis in Logistics:
- Focused Attention: By categorizing items, businesses can focus their attention on the most valuable items (Category A) and ensure they are always available.
- Cost Savings: Efficient management of Category A items can lead to significant cost savings, as these items have the most impact on the bottom line.
- Improved Customer Satisfaction: By ensuring that high-demand items are always in stock, businesses can improve customer satisfaction and reduce lead times.
- Resource Allocation: ABC analysis allows businesses to allocate resources more efficiently, focusing on items that matter the most.
Challenges and Considerations:
While ABC analysis offers numerous advantages, it's essential to consider demand patterns, seasonal demand, and lead times. Additionally, the classification should be reviewed periodically to account for changes in demand or business priorities.
Conclusion:
ABC analysis in logistics is a powerful tool that can transform inventory management. By focusing on items that matter the most, businesses can optimize resources, reduce costs, and improve customer satisfaction. Whether you're a small business or a large enterprise, implementing ABC analysis can lead to significant benefits.
ABC analysis, logistics, inventory management, Pareto Principle, Category A, Category B, Category C, cost savings, resource allocation, customer satisfaction.